The delicate balance of investing today to save in the long term certainly holds true for the forward-thinking management of the Timbadola Sawmill. What gives this balancing act a real homegrown flavour is that the spend was directed at a proudly South African company that produces a uniquely local yellow machine product.

The South African Forestry Company SOC Limited (SAFCOL) is a state-owned company that falls under the Department of Public Enterprises. It has operations in the KwaZulu-Natal, Mpumalanga, and Limpopo provinces as well as in the Sofala and Manica provinces of neighbouring Mozambique.
At the largest sawmill in the Limpopo Province, Timbodola, situated at Levubu, which lies to the east of the town Louis Trichardt, we find Senior Sawmill Manager, Aubrey Kwamba, who holds a qualification in Wood Technology from the Saasveld Forestry College. Aubrey tells us: “This particular sawmill was built around the 1930s and its boilers, commissioned in 1937, are amongst the oldest in the world.
” The Timbodola Sawmill produces mainly structural timber with 85% of its production for the construction industry. The balance is split between an ever-decreasing furniture market and pallet manufacturing. “Our mill processes 120 000 cubic metres of pine timber annually and employs 430 people,” Aubrey explains. “We sell 50% of our production into Gauteng, 40% into the local Vembe district, and 10% across the border into Mozambique.
”SAFCOL sources its timber from its own forests surrounding the Timbodola Sawmill and the company uses its own harvesting and extraction equipment to bring the timber to the roadside. From there it is transported to the mill by haulage contractors. At the mill, contractors were, until recently, used to unload the timber trucks, and sort and stack the logs in preparation for them being fed into the mill.

“As any progressive business does, we analyse our overhead costs on an ongoing basis and we came to the realisation that if we could unload the timber ourselves, we’d be saving money in the long-term,” Aubrey says. “To do this, we realised we’d have to buy cost-effective loading tools.
Aubrey tells a charming story of the company’s oldest Bell Logger, a vintage 125A model dating back to 1970. It had clocked an estimated 50 000 hours and was later named after a retired employee with the surname Savhasa who had operated it for many years. “This answers the question as to why we’ve always relied on Bell Equipment for our timber-handling equipment as longevity coupled with reliability is key in our industry,” Aubrey says. “We own two Bell Wheel Loaders fitted with timber grabs that have served us admirably as well, having clocked 56 000 and 28 000 hours respectively.
” The Timbodola Sawmill owns two 220A Bell Loggers bought in 2010 that are currently undergoing some tender loving care before being put into service again.“We looked critically at rising costs in fuel, labour, utilities, and general inflation and decided in 2020 to review our inbound costs which have the potential to affect us negatively as some timber is sourced from as far as 80km away. Going forward, handling will be insourced by deploying our own timber handling equipment, which will now save us a massive amount of money.”
According to Aubrey, they researched the wider market before deciding on buying three Bell 225F Loggers. Their decision was ultimately influenced by Bell Equipment’s competitive price, their positive experience with previous machines, and above all, the support they knew they could rely on from Bell Equipment’s technical teams in nearby Tzaneen.
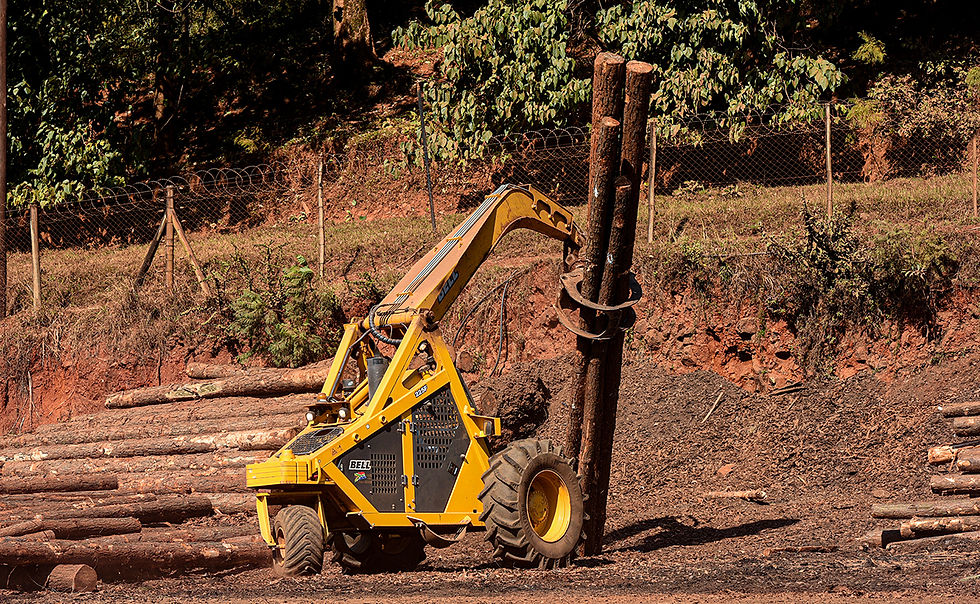
“Soon after we took delivery of the three new Bell 225F Loggers in mid-2022, Louis Fivaz, the new Branch Manager at Bell Equipment Tzaneen, paid us a visit to personally assure us of his teams’ commitment to looking after our Bell-branded equipment and they have done exactly that,” Aubrey says. “We’re happy to say that Bell Equipment’s response times are prompt, and the availability of parts and service kits assure us that we’ll continue to extract long lives from these new Bell Loggers, which certainly have made a positive impact on our production and bottom line.
”The Bell 225F Loggers have been bought with standard warranties of 12 months and unlimited hours. Aubrey mentions that the machines operate in two nine-hour shifts during which they run for a total of 13 to 14 hours, which points to busy production schedules and high utilisation figures. They have been pleased with how much quieter the new Yanmar engines run and the favourable average fuel figures per hour.