SLG – Optimised combustion: safety, efficiency and savings
- Grant
- Jul 7, 2021
- 2 min read
Updated: Jan 31, 2022
You’ve heard it before, ‘costcutting’, ‘project savings’, ‘limited operational expenditure’, ‘do more with less’.
These are common phrases in the manufacturing sector. So what can an organisation do to jump on board the savings and sustainability bandwagon?
As the heartbeat of all operating plants, the procurement and usage of energy attracts the most cost and requires continuous monitoring, analysis, action and improvement.
Organisations need to get the correct people to answer the following imperative questions. How can fuel be optimally used? Are we combusting it correctly? Is the end-use justified and optimised?
Whether its boilers, furnaces, ovens, stentors or even welding applications, all fuel-burning equipment requires monitoring and optimisation, in order to yield the best results.
Safety First
In a combustion reaction, a fuel reacts with oxygen. These reactions transfer energy to the surroundings as light and heat. Combustion safety is paramount and if not conducted correctly, it could lead to a chain of catastrophic events. To ensure safe and complete combustion, excess oxygen needs to be supplied to the combustion process.
Failure to provide sufficient air into the combustion process means that not all fuel will not be burned and, consequently, it will be lost up the stack in the form of combustibles. Not only does this result in an obvious waste of valuable energy, but also presents as a safety hazards, as the possibility of explosions are created.
Fuel Efficiency
On the other hand, when there is too much air in the combustion process, additional fuel is burned to raise the temperature of this excess air to that of the combustion process. Excess air is a costly waste of fuel, because it simply absorbs heat that goes up the stack, rather than being used in the operating process.
Finding the Optimal Balance
The luxury of ensuring that your process receives the correct quantities of air has now become a necessity. The optimum zone of combustion has a small range, so how can one get the right balance?
Firstly, one needs to monitor and analyse the stack or flue gas, by means of a flue analyser. Traditionally this was seen as expensive, however, the development of this technology, have made them affordable. As part of its value-added services to customers, SLG’s flue gas analyser is available to all customers at no cost.
Additionally, coupling the signals from the analysers to that of the fans will ensure that production is in the optimum combustion zone.
Un-optimised combustion can cause industries to spend as much as 10% extra on fuel overheads, which is a massive expense, especially if calculated over a five to ten-year contract term.
Over the recent years, SLG’s gas analyser has enlightened customers on efficient combustion. The analyser has revealed inefficiencies and the potential for financial savings, and in some cases, has highlighted significant safety risks of substoichiometric combustion and carbon monoxide formation.
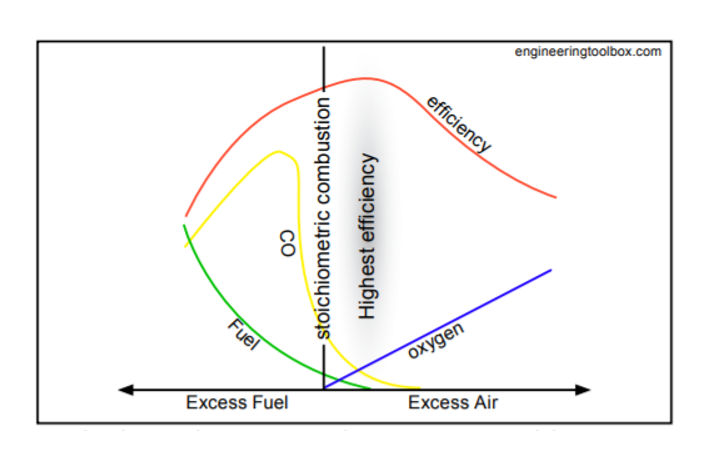
As a reputable gas supplier in the energy sector, SLG not only supplies pipeline and compressed natural gas, but also prides itself in ensuring that its customers use gas optimally. Complementary, value-added services, ensure that all customers are familiar with the full supply chain, the safety and compliance requirements and lastly, the need to ensure allround optimisation.
T: +27 (0)31 812 0555